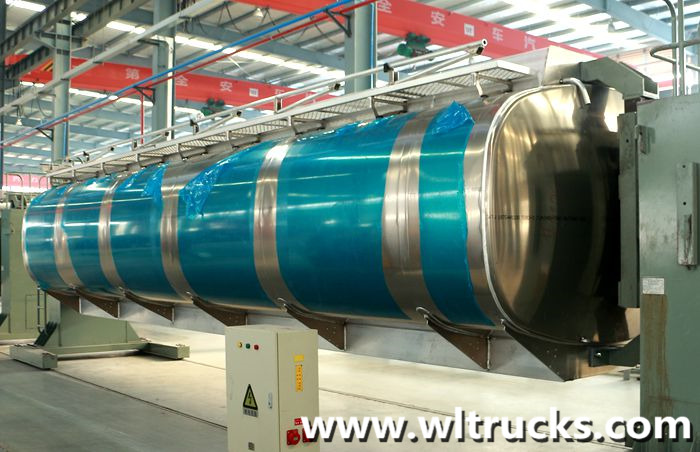
Aluminum alloy Fuel Tank trucks are mainly composed of two parts: chassis and tank body. At present, the commonly used tank body materials are mainly carbon steel, aluminum alloy and stainless steel.
The above figure 1 shows the aluminum alloy tank body , except for the material In addition, another very important factor is the production process, which is why the same configuration, the same tank material, but the price is different, as a tank truck manufacturer, let’s take a look at how aluminum alloy tanks are. maded.
One. Cutting
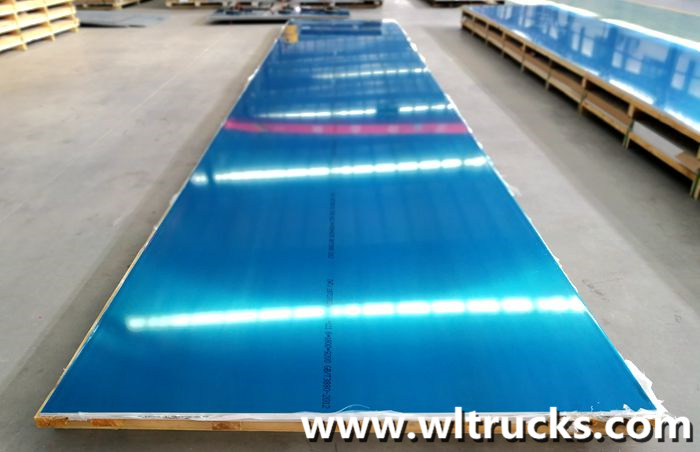
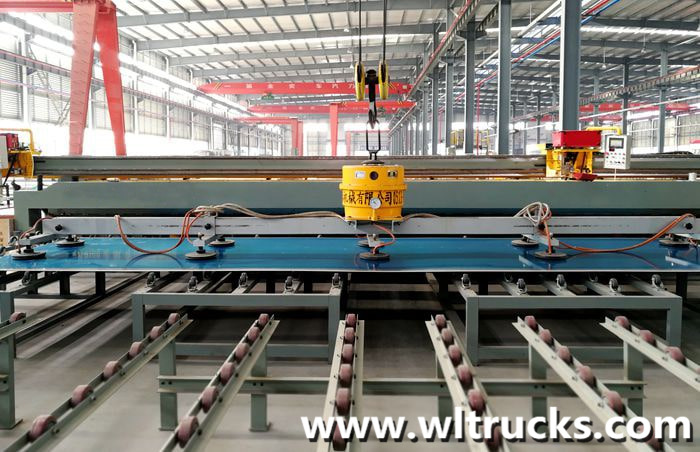
There are specializations in the technical industry. The production of fuel tanker tanks is mainly divided into cylinders, heads, auxiliary beams, tool boxes, etc.
The aluminum alloy fuel tank truck of our company is divided into multiple processes, and each process is equipped with a professional Equipment and professional technical personnel, the advantage of this is that professionals can do professional work and workmanship can be more refined.
The tank body is made of 5083 aluminum alloy (Figure 2). The aluminum plate is cut into a size that meets the national announcement standard by a cutting machine (Figure 2). 3);
two. Roll can
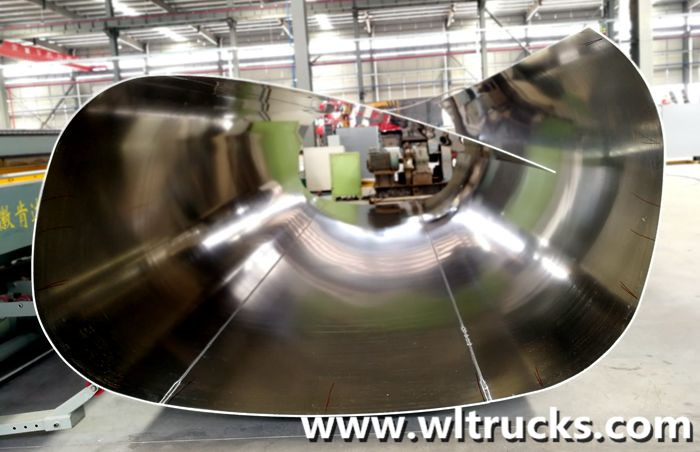
The barrel of the tanker is the core material of the fuel tank truck. The amount of fuel is determined by the size of the barrel. The aluminum alloy barrel is made of 6mm thick material.
The aluminum alloy sheet needs to be rolled after being cut to standard size. (As shown in Figure 4), multiple aluminum alloy plates are connected together by a can coiling machine and fixed by double-sided welding;
three. Head production
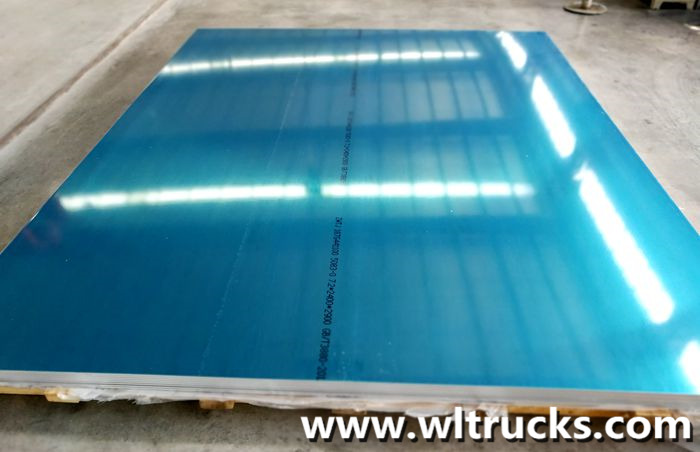
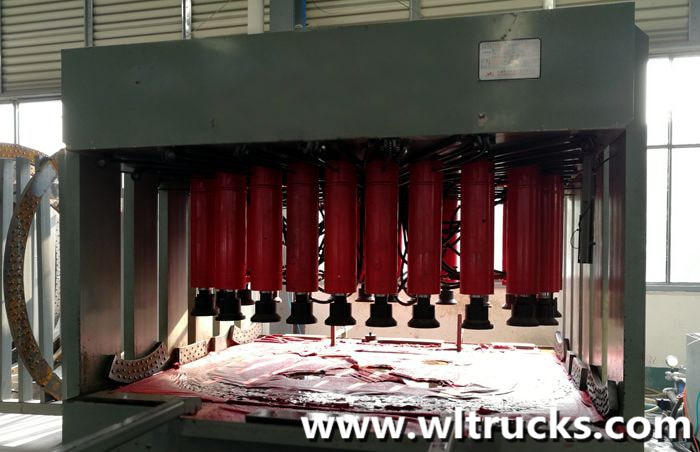
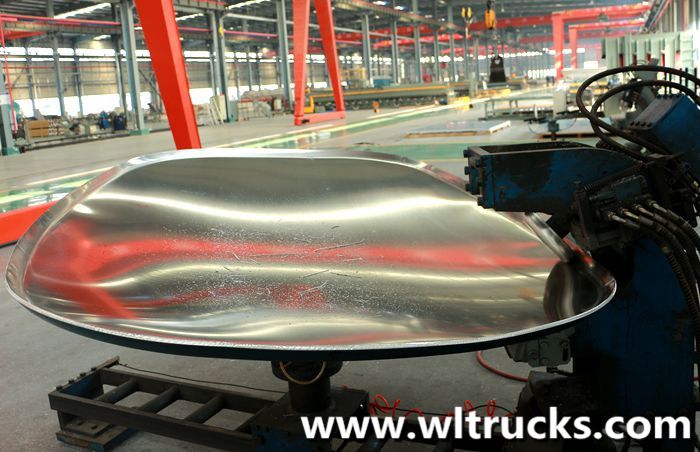
After the tank body is welded, look at the process of the head. The aluminum alloy head needs to resist the impact of the oil on both sides of the tank body (that is, the head) during the vehicle transportation.
Therefore, the aluminum alloy tank head It is 1mm thicker than the cylinder, which is 7mm thick material (as shown in Figure
5). The production of the head needs to be cut into a circular shape by a cutting machine. Since the head and the cylinder are connected by double-sided welding, the shapes of the two The size must be able to match, and the requirements for the head are relatively high. We use a plasma cutting machine to cut into the shape required by the drawing, and then shape the shape by a bulging machine (as shown in Figure
6), and finally use a hemming machine to cut the head The edge is made about 6cm deep (as shown in Figure 7);
four. Production of wave breaker
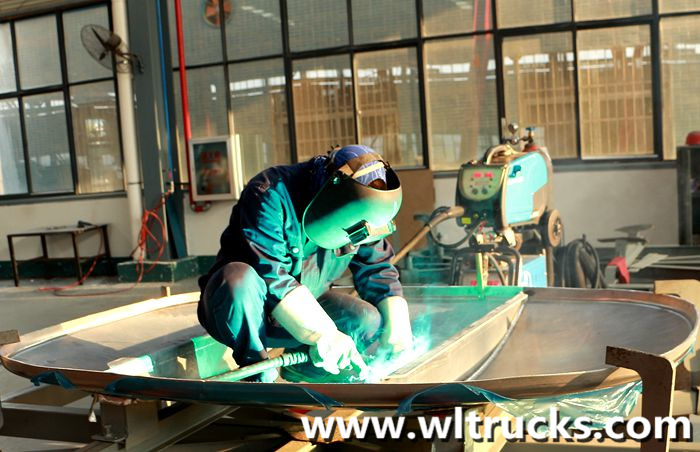
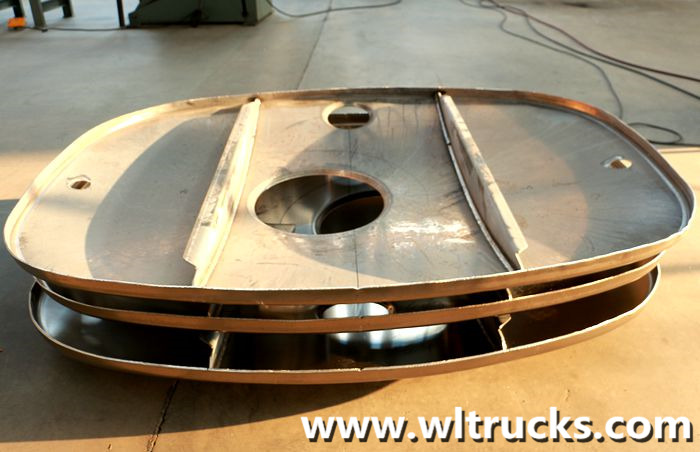
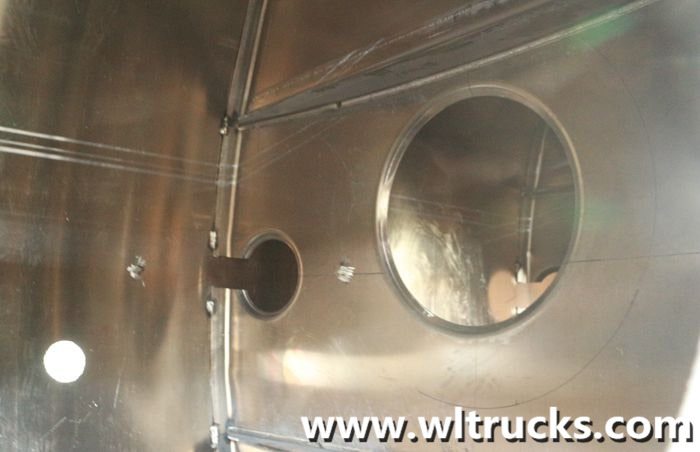
During the transportation of the Aluminum alloy fuel tank truck, the oil will have an impact on the tank body due to the flow, especially when going up and down slopes, which will affect the transportation safety.
The production of the wave breaker can reduce the impact on the two side seals and the tank body. It can prevent the tank body from deforming. According to the size of the tank body of the tanker, multiple wave breakers will be designed.
The production of the wave breaker and the head is somewhat similar. According to the drawings, the required shape is made by the plasma cutting machine and the edge machine.
A number of manholes of different sizes are cut on the anti-wave board, arranged in a staggered arrangement, and two fixed plates are welded (as shown in Figure 8, Figure
9) to enhance the strength of the anti-wave board. Finally, the anti-wave board and the cylinder For welding, double-sided full welding is used (Figure 10) to enhance the fixing strength and stability.
Fives. Tank welding
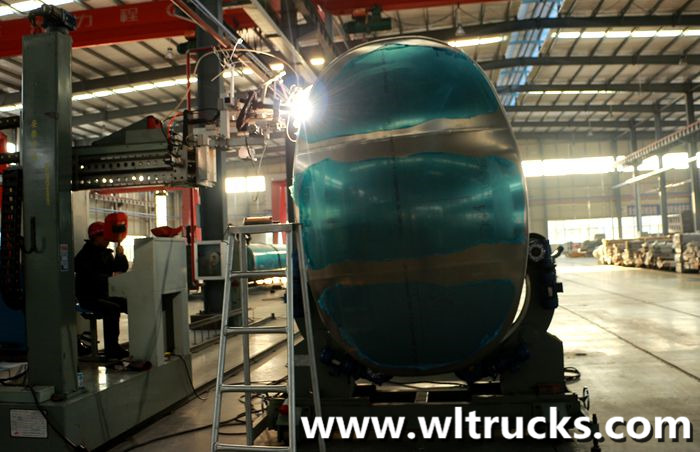
The tank body of the oil tanker is fixed and changed to an appropriate angle by a rotating machine, and the machine is automatically welded (as shown in Figure 11), and double-sided welding is adopted. Through electric control, remote monitoring is used to avoid missing welding.
six. Install toolboxes, protective fences, etc. to form a complete vehicle
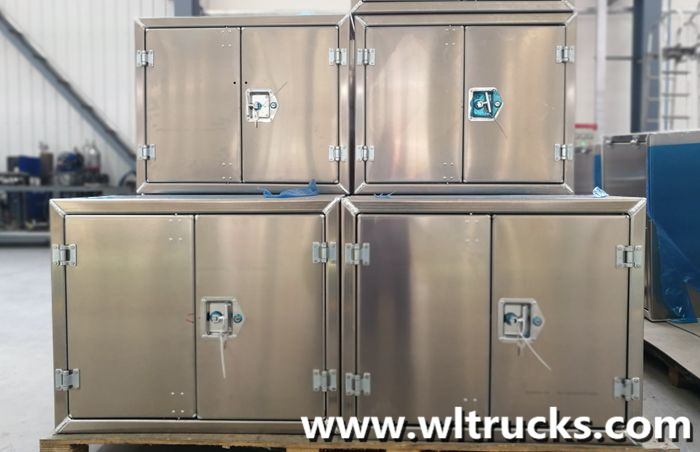
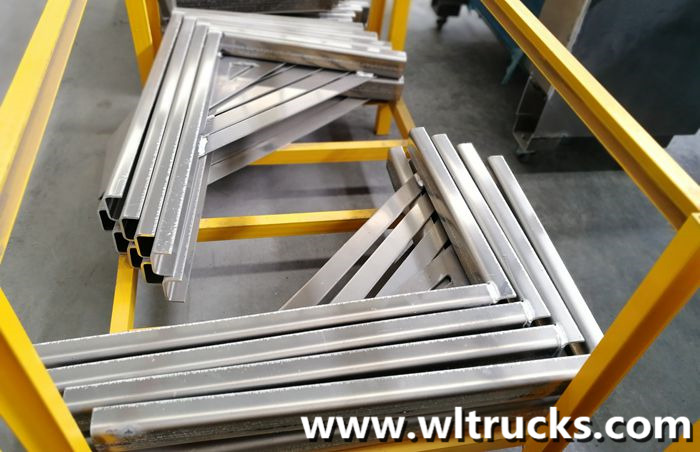